Copyright 2025 Robert Clark
In the blog post “Reentry of orbital stages without thermal protection, Page 2”, http://exoscientist.blogspot.com/2025/04/reentry-of-orbital-stages-without.html , I discussed some possibilities of thermal protection for the SpaceX Starship. Chief among them was the possibility that lightweight wings added might allow the stainless-steel Starship to survive reentry without added thermal protection at all.
Other possible methods of thermal protection discussed there were a “parashield” of Dr. David Akin and inflatable conical shield experimented for the Cygnus capsule return.
The method used there to estimate the temperature reached was calculation of the ballistic coefficient,
β = (mass)/(drag coefficient*area). In a report by aerospace engineer Dr. David Akin, the estimated ballistic coefficient for the max temperature reached to be 800 C, so as not to need additional thermal protection, was ca. 20 kg/sq.m.
However, I calculated the ballistic coefficient for the Starship to be ca. 60 kg/sq.m. Note though this was using a much lower dry mass for the Starship than now obtains. The currently estimated dry mass of the reusable Starship is in the range 160+ tons. I believe this high mass for the reusable Starship is primary reason SpaceX is having difficulty getting effective TPS for it.
My opinion is that SpaceX should first get an expendable Starship and then proceed to reusability. This approach worked spectacularly well for the Falcon 9.
In this regard it is notable Elon Musk once estimated the dry mass of the expendable Starship as only 40 tons:
Elon Musk @ElonMusk
Probably no fairing either & just 3 Raptor Vacuum engines. Mass ratio of ~30 (1200 tons full, 40 tons empty) with Isp of 380. Then drop a few dozen modified Starlink satellites from empty engine bays with ~1600 Isp, MR 2. Spread out, see what’s there. Not impossible.
https://x.com/elonmusk/status/1111798912141017089?s=61
Then in the following I’ll use the 40 ton value for the Starship dry mass. In this case, there might be an example that would give us a reusable thermal shield for a vehicle the size of Starship. I’m thinking of the X-33/Venturestar.
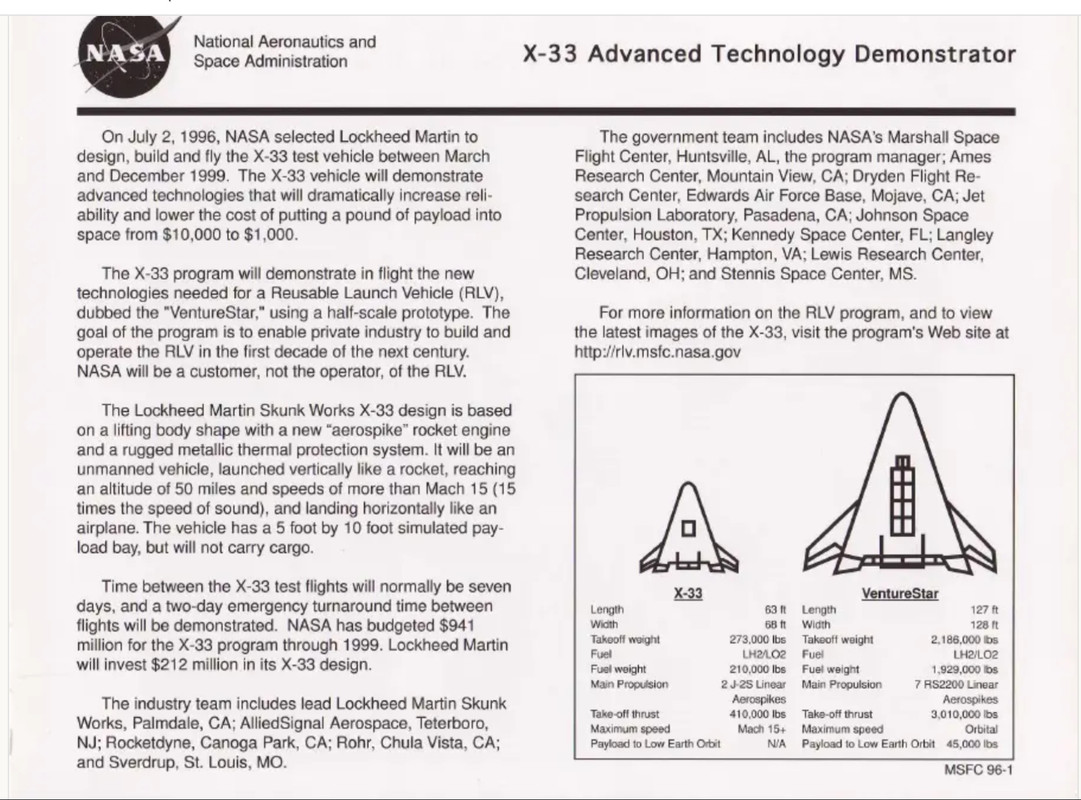
The length in meters was 38.7m and width 39m. For the dry mass, the total gross weight was 2,186,000 lbs, propellant weight 1,929,000 lbs, and payload weight 45,000 lbs; giving a dry weight of 212,000 lbs, or 96,400 kg.
Using a hypersonic drag coefficient of 2, and considering the triangular planform requires multiplying by 1/2 the length*width to get the area, the ballistic coefficient calculates out to be 96,400/(2*1/2*38.7*39) = 64 kg/sq.m.
Remarkably close to the ballistic coefficient of the Starship at the 60,000 kg mass of the expendable’s dry mass + fairing mass.
But the added weight of the metallic shingle TPS of the X-33/Venturestar can’t be too high to allow the ballistic coefficient to remain close to this value.
The areal density of the metallic shingle TPS was about 10 kg/sq.m:
REUSABLE METALLIC THERMAL PROTECTION SYSTEMS DEVELOPMENT
Max L. Blosser*, Carl J. Martin*, Kamran Daryabeigi*, Carl C. Poteet **
*NASA Langley Research Center, Hampton, VA, USA
** JIAFS, The George Washington University, Hampton, VA, USA
https://ntrs.nasa.gov/api/citations/200 … 095922.pdf
The metallic tiles had better resistance to impact and rain than the ceramics at about the same weight.

Fig.3 Layered metallic sheeting separated by insulation.

Fig.21 Metallic TPS at same weight of ceramic tiles, ~10kg/sq.m.
At a 10 kg/sq.m. areal density, the added weight covering just the lower half of the Starship would be (1/2)*Pi*9*50*(10 kg/sq.m.) = 7,060 kg, proportionally small enough that the ballistic coefficient would still be ca. 60 kg/sq.m.
This would be advantageous in that you don’t need added wings and you don’t need an additional conical thermal shield.
BUT for this to work SpaceX would have to go back to the smaller, expendable mass of the Starship. SpaceX had tested the X-33 metallic shingles and concluded they were inadequate. But that was with temperatures developed with the higher 160+ ton Starship. With a lighter dry mass, much reduced temperatures result.
Thermal Protection for the Falcon 9 Upper Stage.
SpaceX had originally intended to make the Falcon 9 upper stage reusable as well as the first stage but decided it was too difficult and chose to only make the first stage reusable. They also engaged in attempts to recover the separated fairing half’s, but decided not to continue implementing this.
However, the metallic shingles of the X-33/VentureStar may provide a method to recover the upper stage and fairing.
This page gives the F9 upper stage as 12.6m long, 3.66m wide at a dry mass of ~4,000 kg, and the fairing as 13.1m long, 5.2m wide, at ~ 1,750 kg:
Falcon 9 FT (Falcon 9 v1.2)
https://web.archive.org/web/20230710234357/https://spaceflight101.com/spacerockets/falcon-9-ft/
The interstage has been estimated as weighing 1,000kg. Then using again a cylinder’s hypersonic drag coefficient of 2, the ballistic coefficient calculates out to be:
(4,000 + 1,750 + 1,000)/(2*(12.6*3.66 + 13.1*5.2)) = 29.5 kg/sq.m.
This is well less than the desired 60 kg/sq.m point for metallic shingle TPS. But we have to make sure the added weight of the TPS still allows the ballistic coefficient to stay below this point.
The weight of this added metallic shingle TPS would be (1/2)*Pi*(12.6*3.66 + 13.1*5.2)*10 kg/sq.m. = 1,800 kg. Adding this on, the ballistic coefficient would still only be 36 kg/sq.m.
Another possibility though arises from the low ballistic coefficient of 29.5 kg/sq.m from the bare upper stage+fairing without TPS. This is close enough to the 20 kg/sq.m ballistic coefficient point for a stainless steel spacecraft not needing TPS, that should be investigated for the F9 upper stage.
The tankage, fairing, and interstage would have to be replaced by stainless-steel. The tanks are aluminum-lithium. The specialty high-strength stainless-steel as used on Starship saves about 1/3rd the weight off aluminum-lithium tanks. But the fairing and interstage are composite. The stainless-steel alloys are about the same weight as the carbon-composites.
Doing some rough estimates it will be approx. at the 20 kg/sq.m point if the tanks and fairing are converted to stainless-steel but the interstage is jettisoned and just use a lightweight steel plate to block the engine from the high temperature air stream during reentry.
No comments:
Post a Comment